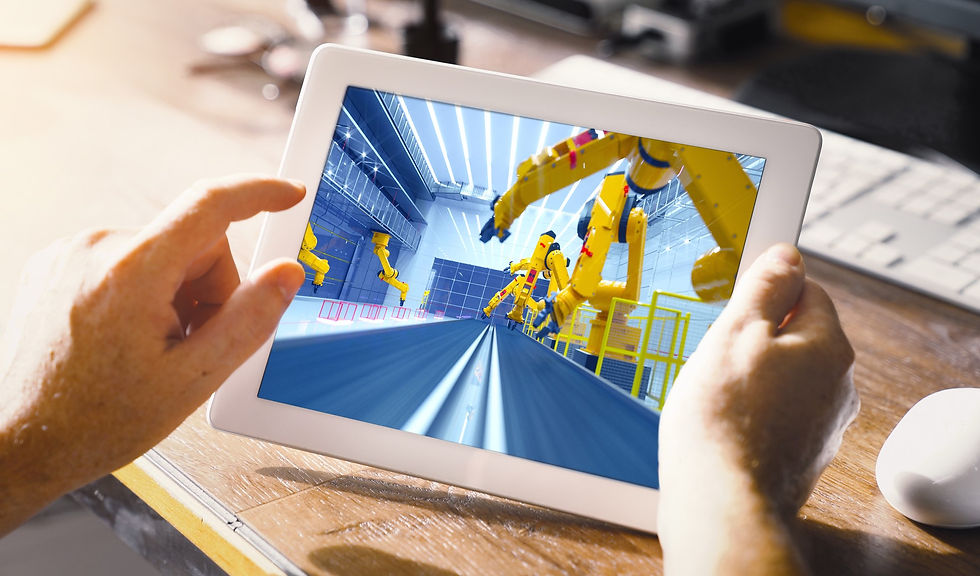
You already know that we are in the middle of the fourth industrial revolution. You have already started transitioning to a smart factory model. But, is your smart factory smart enough?
Technology is changing fast. If you aren’t continuing to update and upgrade your different systems, your smart factory can go from cutting-edge to obsolete in the blink of an eye. A smart factory that is smart enough to keep you ahead of the competition will have these five components:
Deep Automation
Real-Time Integration
Advanced Sensor Technology
Machine Learning
Remote Operations Capabilities
Your smart factory must have all 5 of these different components.
1. Beyond Basic Automation
Having a handful of robots on the factory floor does not mean you have a smart factory. You need to go beyond basic automation. Your factory needs to be using robotics in a deep way.
The most successful smart factories have cooperative robots, or cobots, that work alongside your employees seamlessly. They have robots that can do more than a single, preprogrammed task.
Deep automation means that your robotics and other systems can change as new data becomes available without needing additional human input.
2. Real-Time Integration
In a smart factory, production, pricing, shipping, and receiving are all integrated in real-time. Your systems and machines are linked together so that a change in one part of your operations automatically triggers needed changes in other parts of the operation.
The best smart factories are nimble because they make changes at the speed of the internet, not the speed of human intervention.
Even small changes in your supply chain are analyzed in real-time by the rest of your operations, and any adjustments to production schedules and pricing are automatically factored into future operations.
Integration is more than just communication. It’s communication with automated action.
3. Advanced Sensor Technology
The heart of a smart factory is the ability of machines, robots, and systems to communicate with each other. The collection, processing, and analysis of data is made possible by a network of advanced sensors.
At every point in the operations of a smart factory, sensors allow for the automation of everything from inventory management to shipping and receiving. Advanced sensors detect a variety of changes to the rest of the system.
Sensors that measure weight and quantity are often used in factories to automate portions of the manufacturing process.
But, advanced sensors can detect changes in machine performance due to environmental changes, computer processing needs, and proximity to humans. These advanced sensors help keep your robots working at top efficiency and extends their useful lifecycle.
Advanced sensors also allow robots to safely work in closer proximity to your employees.
4. Machine Learning and Advanced Data Analytics
Raw data is critical to the operation of a successful smart factory. The data is only useful if you also have the ability to analyze the data and make decisions based on the results.
The best smart factories take advantage of potent machine learning algorithms to automatically make adjustments based on the results of advanced data analytics without needing humans to reprogram any of the machines or robots.
Advanced data analytics and machine learning make it possible for your factory to maintain productivity levels, even when there are disruptions in your supply chain.
5. Remote Operations
Smart factories do not require a large contingent of humans onsite to monitor progress or make adjustments. Instead, the ideal smart factories can largely be managed remotely.
Having remote operations capabilities lowers costs, improves productivity, and gives your business the flexibility to adapt to changes caused by pandemics, natural disasters, or labor market upheaval.
If you want to stay competitive, your smart factory must be smart enough to adapt to any changes in the market in real-time.

Comments